Sustainable Manufacturing: Transforming Industries for a Greener Future
The concept of sustainable manufacturing is defined as the introduction of green practices in the production of any type of good or product. The manufacturing sector is among the top three causes of harmful gas emissions to the planet. This is why it is essential to apply these clean techniques throughout the manufacturing process.
In fact, sustainable manufacturing is so powerful that more and more companies are adding their own sustainability goals to the production as a measure of quality in all their operations.
Throughout this article, we will explain everything about green manufacturing: what it is and how it applies to industry, what its benefits are, the possible difficulties in applying it and even review its evolution and future trends.
What is Sustainable Manufacturing?
Sustainable manufacturing is a discipline that encompasses numerous practices, all of which have a common goal: to improve efficiency and reduce waste in any industrial manufacturing process. It involves a holistic approach to manufacturing, which is defined by the following elements:
- Economic viability: It is essential that sustainable manufacturing is economically viable, which means optimizing the use of resources while implementing a business model that integrates the circular economy.
- Environmental protection: Sustainability in production involves reducing emissions, effluents and waste, with the aim of preserving our planet’s natural resources.
- Social responsibility: This issue implies social responsibilities towards local communities. Therefore, it is also crucial to positively influence local communities by practicing ethical labor standards and contributing sustainably to the local economy.
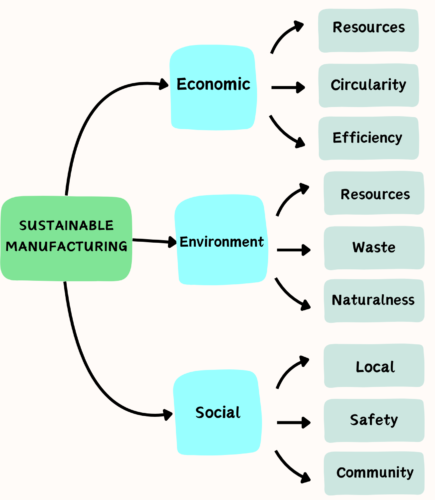
Key Strategies for Implementing Green Manufacturing
Designing eco-friendly manufacturing systems involves optimizing the use of natural resources through sustainable manufacturing technology. In other words, we must apply to industry the three points defined in the previous section: economic viability, environmental protection and social responsibility.
These three characteristics are giving rise to green manufacturing and Industry 4.0, two very interesting concepts that encompass the technological evolution of product manufacturing. The following table summarizes the different sustainable manufacturing solutions.
Resources | Technology | Logistics |
---|---|---|
Sustainable Product Design | Upgrade Production Equipment | Local Production |
Sustainable Sourcing | Smart Manufacturing (Industry 4.0) | Reduced Inventory |
Self-Healing Materials | Process Simulation (Digital Twins) | Efficient Transportation Routes |
Energy Monitoring and Optimization | Operating Robots and Automated Machines | Implement Green Warehousing Practices |
Although there are always new ways to make industrial processes more efficient and cleaner. So it is important not to limit yourself to the tactics mentioned above. Personally, we recommend contacting expert consultants in the field to get the most out of each case.
Benefits of Sustainable Manufacturing
Next, let’s talk about the benefits that can come from applying sustainable practices to product manufacturing. Some may seem fairly obvious, but others may surprise you:
- Environmental protection: Environmental protection and conservation is a direct consequence of applying sustainable practices and polluting less.
- Cost savings: Making efficient designs, using renewable energy and minimizing waste means significant cost savings.
- Long-term viability: A company that thinks about sustainability at all levels will achieve long-term results.
- Regulatory compliance: Complying with sustainability and Corporate Social Responsibility (CSR) regulations saves unwanted fines.
- Enhanced brand reputation: Growing economically while putting the well-being of the planet and society first improves public image and customer loyalty.
- Catch up on consumer trends: More and more companies are embracing sustainability, as implementing sustainable production systems enhances the vision of any brand.
It is clear that adapting a sustainable manufacturing model is neither easy nor cheap, but companies that want to grow in the long term need to make the change to survive in today’s world.
Case Studies: Companies Leading the Way
More and more companies of all types and sizes are turning to sustainability. From large logistics companies like Best Buy to small industrial companies that manufacture any type of product. This is giving rise to the concept of Net-Zero companies.
A Net-Zero company is neutral in terms of polluting emissions. For a company to be Net-Zero, it must ensure that all its contaminant activities are no longer polluting, from manufacturing to logistics and product sales.
We will now take a look at a couple of large companies that have committed to becoming Net-Zero in the coming years. These two companies belong to two very different industries, which is a clear indicator that sustainable manufacturing companies are possible in all sectors.
Etsy is Committed to Net Zero
Etsy is one of the largest shopping websites on the Internet, and is the first one to neutralize carbon emissions from shipping and packaging each delivery. But, as they detail on their impact page, they want to be Net-Zero by 2030.
Siemens is Going Net Zero
Electronics manufacturer Siemens hopes to be Net-Zero by 2030, which is astounding given the current size of this company. On their sustainability page, they detail their goals and how they are applying technology to reach zero-emission status.
Challenges of Green Manufacturing
Like everything else, sustainable industrial manufacturing has its drawbacks, or rather, initial difficulties. But, when these hurdles are overcome, there are great advantages, as sustainable business models add up to many benefits in the long run, which have been detailed above.
For the vast majority of businesses, the initial challenges they may face are related to the large upfront costs of making a transition in the production system, and their respective resistance to change. Clearly, making the transition to sustainable production is neither cheap nor easy, but it is highly desirable.
What many businesses fail to realize is that you don’t have to start by building a sustainable factory, you can start with much less. Moreover, many times a company’s own production efficiency issues can dictate the transition to sustainability.
For example, a company may want to improve its profit margins, which can be achieved by setting performance benchmarks. These, in turn, lead to greater efficiency and, therefore, a cleaner production system.
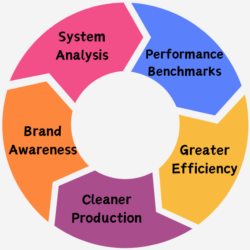
FAQs about Sustainable Manufacturing
Next, we will answer some questions related to the application of green manufacturing practices. If you have any doubts at the end of this section, feel free to leave us a comment and we will answer any remaining questions.
What are the main goals of sustainable manufacturing?
The goals of sustainable production are to reduce environmental impact, ensure economic performance and promote social responsibility. This is achieved by implementing the strategies described in the table above.
How can small businesses adopt sustainable manufacturing practices?
Local businesses can adopt sustainable practices, starting by applying some of the more cost-effective methodologies discussed above. Every business is different, but we recommend starting with sourcing more sustainable suppliers, switching production systems to renewable energy, reducing inventory through universal designs and applying sustainable logistics methods.
It is also a great idea to redesign products with the principles of the circular economy in mind, to ensure that they are durable, repairable and recyclable at the end of their useful life.
What role does technology play in sustainable manufacturing?
Technology enables production systems to be more efficient, thus saving costs and reducing emissions by applying sustainable manufacturing processes to minimize waste and pollution. Additionally, technology enhances system monitoring, leading to fewer safety risks.
In supply chain management, retrofitting process plants for sustainability at every production stage and using sustainability-minded suppliers are essential for achieving comprehensive sustainable manufacturing practices.